Torbjörn Idhammar, President, IDCON INC
Part 2 in this series covers how Preventive Maintenance fits into the overall Reliability and Maintenance cycle. Figure 1 shows IDCON’s Productivity Circle which is used to demonstrate the overall partnership between Operations and Maintenance.
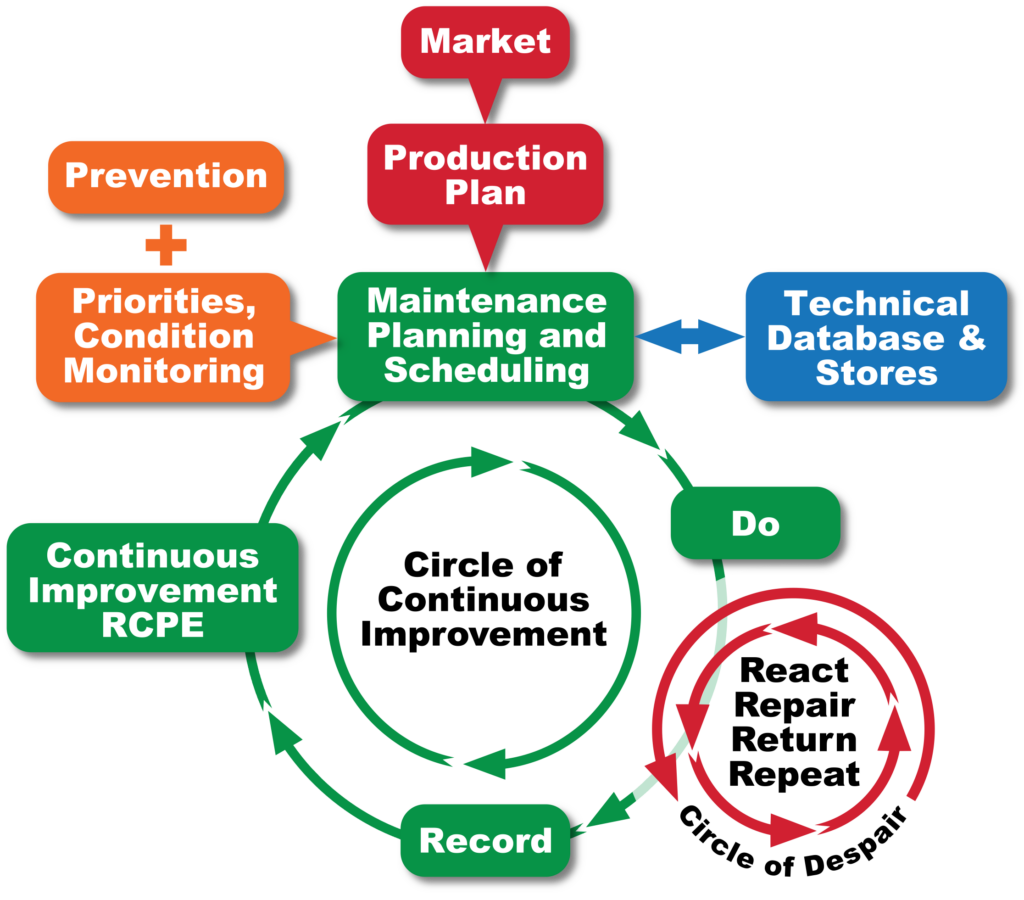
Following IDCON’s Productivity Cycle for Continuous Improvement
If your organization’s product has been picked up by the market, the next step is to form a production plan. This production plan must be integrated into Maintenance Planning and Scheduling. Once the work is planned and scheduled, it is executed and recorded in the Computerized Maintenance Management System. Continuous improvement can be achieved through doing research with a Root Cause Problem Elimination (also known as Root Cause Failure Analysis).
Prevention and Priorities/Condition Monitoring and Technical Database and Stores
In Figure 1, the boxes “Prevention” and “Priorities, Condition Monitoring” as well as “Technical Database and Stores” are connected to Maintenance Planning and Scheduling.
Creating a good technical database and having an organized storeroom make it possible to find parts, tools, and documentation.
In order to plan and schedule, a Preventive Maintenance process must be in place. “Prevention” done correctly will ensure that work never gets requested for a piece of equipment. “Condition Monitoring” refers to finding failures early. If failures are found, work is planned and scheduled.
Help your organization improve Developing and Managing Preventive Maintenance with IDCON.
The Chain that Must not be Broken
At IDCON we like to say “keep it simple” – so let’s break down the Productivity Circle further.
In the first box is “Prevent.” Preventive Maintenance is the base of good Reliability and Maintenance. Preventive Maintenance tasks to prevent failures include lubrication, good installation and operating practices, among others. If these tasks are performed correctly, there will always be less work in the backlog, and your organization can avoid costly unplanned downtime, unscheduled shutdowns, and equipment breakdowns.
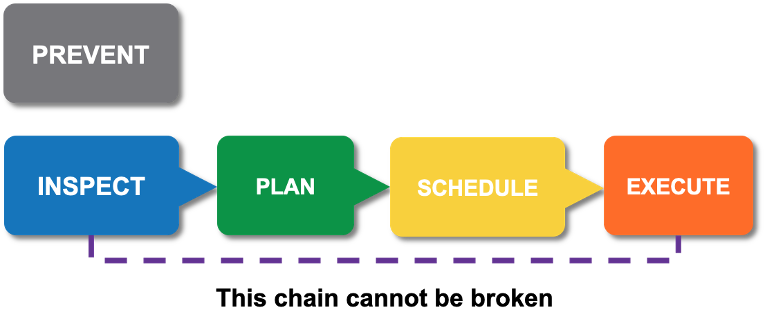
Prevention is the first step in what IDCON calls “the chain.” The next step is “Inspect” which refers to Condition Monitoring inspections. These include subjective inspections such as look, listen, feel and smell as well as objective inspections using a condition monitoring tool such as an infrared camera or vibration pen. Again, Condition Monitoring is the basis of good Reliability and Maintenance.
Make sure your Operators are trained in basic inspection techniques.
The Purpose of Preventive Maintenance
After Condition Monitoring inspections, it is time to plan, schedule and execute the work. This chain contains everything that is the purpose of Preventive Maintenance – to prevent failures and set up the planning and scheduling process when work does need to be done. Good Preventive Maintenance creates the opportunity to extend equipment life and work more efficiently by completing repairs safely, on time, and at a high quality.
Watch Tor’s video related to this article on our YouTube Channel.
Torbjörn Idhammar is president and CEO of IDCON, Inc. and section editor, Reliability & Maintenance, for Paper360° magazine. Contact him at [email protected]. For more articles, please visit: www.idcon.com and www.maintenanceworld.com.