The global tissue industry has seen a lot of dynamic changes lately, with new projects being announced, acquisitions and expansions, as well as divestments. However, there is underlying uncertainty worldwide due to politics and regional conflicts which will certainly affect business decisions going forward. Tissue360° spoke to Bodo Kottwitz, industry consultant, about all things tissue around the world.
“At no other time that I can remember has politics become so important to the decision making in the global tissue industry,” says Bodo Kottwitz, owner of BKay Tissue Advice, based in Germany. “The regional conflicts we see in Ukraine, the Middle East, and then looking forward to what China may or may not do with Taiwan, have brought an atmosphere of instability that we haven’t see for many years.”
Kottwitz continues: “In Europe, there are a number of challenges, including energy costs due to the war in Ukraine, low demand and overcapacity. Moreover, the industry has still not got back up to the pace before the pandemic. The year 2023 could have been a lot better for tissue companies as it started in a promising way with a high shelf price level of tissue products and decreasing fiber costs. However, all other circumstances—especially the demand in the context of high inflation and insecurity—made it hard for tissue producers in the region to produce profitably, especially when operating in the commodity space of bathroom tissue and kitchen roll. In 2023, demand was likely shrinking and the producers were fighting for sales. It was not a year that the tissue industry was able to catch up financially and strengthen again.
“It wouldn’t surprise me if we see some movement in the selling of some major assets in Europe in the near future. We might even see tissue machine shutdowns as it becomes clear that companies can improve their situation by importing parent rolls and converting rather than making the tissue themselves; I know of more than one company that is already looking into this.”
Kottwitz says that the secret of survival for vulnerable companies lies in specializing in more niche areas, improving the margins and getting away from the commodity areas. This does not necessarily mean niche categories, but also “alternative paths”; for example, an all-regional product or products based on smart alternative raw materials. “Also, companies need to tighten up when it comes to economies of scale, purchasing behaviors, and production and converting efficiencies, as well as finding ways around the energy price challenges.”
THE UK, A SPECIAL CASE
The UK seems to be something of a hot spot in the tissue market currently with a raft of developments going on, including a new mill development by Metsä Tissue, Wepa Group’s recent acquisition of Star Tissue, and the proposed tissue mill at UPM’s former site at Shotton by Eren, part of the Modern Karton Group. There are also movements at ICT, Fourstones, plans for Accrol, as well as the possibility of further developments in the pipeline.
Metsä Tissue has recently announced the location of its new mill in the UK at Goole in the north of England, where the plan is to eventually produce 240,000 metric tpy of tissue in phases over the next decade. Eren Paper announced in 2021 that it will build new tissue lines at the Shotton site with a capacity of 210,000 metric tpy along with containerboard. The UK currently imports around 45 percent of its tissue consumption, so these two projects will certainly be aimed at domestic need.
So why so much activity in the UK? Kottwitz says, “The UK is a case out on its own in terms of the survival of standalone converters and attractiveness for new mills, even with the Brexit effect. The planned aggregated enormous capacities of Eren/Modern Tissue and Metsä Tissue could be locally absorbed if jumbo roll imports could be substituted—but would they really? Both companies are planning converting facilities, and this means not only substitution of imported jumbo reels, but gaining market share from operating companies.
“Unlike the Europeans, UK retailers as well as AfH customers have embraced non-integrated tissue converters as strong suppliers and business partners. This might be one of the reasons for the Wepa deal with Star Tissue rather than organically increasing its AfH business.”
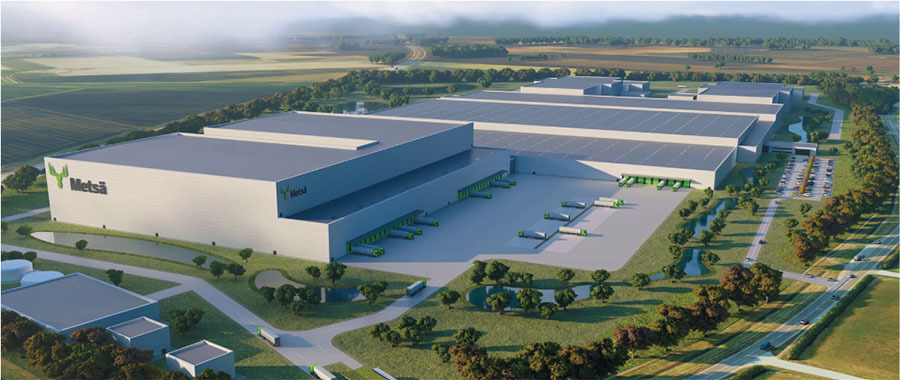
THE US: BACK TO NORMAL
The US has seen a number of investments recently, including the latest one by Sofidel through its acquisition of ST Paper’s mill in Duluth, Minnesota. The mill comes equipped with the latest technology, including an Andritz tissue machine which was only started up a year ago and can produce 65,000 metric tpy. The company is also pressing forward with its expansion of its integrated plant in Circleville, Ohio, which will see a new Valmet machine increasing mill capacity to 200,000 metric tpy and making the mill Sofidel’s largest in the group.
Georgia-Pacific has also recently announced a further $150 million investment at its Halsey facility in Oregon. The mill has already seen a recent investment of $50 million and will bring online a new tissue machine and converting assets by 2025.
“In the US the market is in better shape than in Europe. The AfH market in particular has significantly improved since the pandemic as it seems Americans are going out a lot more for entertainment when compared with Europeans. Also, offices in the US are mostly back to work after COVID-19, which means higher demand in the workplace. And the economy has picked up surprisingly well compared with Europe.”
Commenting on Sofidel’s rise in the US, Kottwitz says, “From a shaky start a few years ago, Sofidel’s move into the US has been highly successful. The company had a bit of luck when the pandemic came along and demand for consumer tissue products went through the roof, and it hasn’t looked back since. The market seemed to appreciate the quality of products, even from consumers who used to be loyal to branded products.
“Sofidel is definitely accelerating the trend toward private label consumer products and is growing stronger all the time. The acquisition of the Duluth mill provides an immediate capacity increase to fill Sofidel’s converting demands, using the market momentum, without the burden of waiting for its next tissue machine to start.
“The company has an excellent strategy of acquiring and then investing, and it has the courage to implement the latest technology to achieve maximum efficiency. It also has an excellent strategy when it comes to environmental, social, and corporate governance (ESG), which gives it an advantage when it comes to customers as well as investors.”
ASIA: CURTAILED DEMAND
Asia, especially China, is seeing lower overall expected economic growth, which is affecting domestic demand, although it seems that some companies are still able to export parent reels around the world at a lower cost than the market price. Again, political decisions come into play in the region.
Kottwitz says, “There is a big question mark on where Russia’s natural gas is going now. It could well be that Chinese and other Asian producers are now benefiting from lower prices as Russia’s fossil fuels have to go somewhere, which will obviously give the Asians producers an advantage.
“It could be that Asian producers will be able to produce much more cost effectively and, therefore, send parent reels to the West, or even more finished products than they send currently. However, this could all change dramatically in the future as the world waits to see what happens between China and Taiwan. We could see a situation where all Chinese imports are banned, which would mean a dramatic shift in the US market, which imports a lot of Chinese tissue products.”
Kottwitz continues, “And the current conflict in the Red Sea already shows a significant impact on container prices from Asia to Europe—when they cannot use the Suez Canal.
“Another interesting move was the sale of Essity’s 52 percent share in Vinda to a subsidiary of April while the divestment of part of the European private label business failed. Essity seems to be focusing more and more on segments outside the (consumer) tissue business, for instance, in the medical and hygiene spaces.”
SOUTH AMERICA: NEW PROJECTS IN BRAZIL
The Brazilian tissue industry in particular is seeing a lot of activity, particularly in the case of pulp producers. Most notably, Suzano and Bracell are both investing or have invested hugely in this space. Suzano recently announced an R$650 million ($133 million) investment in a tissue mill in Espírito Santo that will produce 60,000 metric tpy to come on stream in 2026. Bracell is in the process of starting up its new tissue mill right next to its new Project Star pulp facility in São Paulo state. The company describes the mill as the “biggest and greenest pulp mill in the world.” The tissue mill, currently being commissioned and in start-up, has four of the latest tissue machines from Andritz, which will produce 240,000 metric tpy of tissue for the domestic and South American market.
“At first I was surprised about the move by Brazilian pulp producers and their entrance into tissue,” says Kottwitz, “but it seems a financial business model has emerged that makes perfect sense. There are government bonuses for the exporting of pulp, which makes investing more attractive and less expensive than any other region, and having a tissue plant right next to a pulp mill has a lot of advantages when it comes to energy savings, fiber supply, and pulp logistics. And it has become very feasible to meet most tissue segment quality requirements with 100 percent eucalyptus pulp.
“This new business model could well be a game changer for the industry in the region, and further on to other South American countries.”
NEW TECHNOLOGY TO THE RESCUE? ENERGY SAVINGS AND GOING DIGITAL
Tissue producers are under the hammer, particularly in Europe when it comes to energy volatility, which makes the R&D side of the industry even more important. Suppliers to the industry play a vital role in helping customers reduce energy costs and improve efficiencies, so they can not only survive, but thrive.
There has been a lot of work going on behind the scenes by all the major suppliers. Lately, a series of partnerships have emerged that could see some major changes in how the industry approaches tissue production, particularly when it comes to environmental and efficiency goals. Voith has teamed up with Essity, Valmet with Metsä Group, and Andritz with Sofidel to work on combined projects to address the challenges.
Voith and Essity are working on the development of a new concept that they say will revolutionize the tissue making process. Kottwitz says, “The two companies are collaborating on a disruptive technology that will see a reduction of energy in the production process of 85 percent and cut water consumption by 95 percent. This is at the lab scale currently, but it could be an exciting development to look out for because it is totally new.
“Along with the new developments at Voith and Essity, Valmet and Metsä Group are teaming up to create a model to address various aspects of sustainability related to ESG on projects. Andritz is working with Sofidel on energy projects using bio-syngas. This all represents a new era of partnerships in R&D that will only push the industry forward,” Kottwitz adds. “Another development to look closely at is Toscotec’s all-electric tissue mill, which is really interesting as it could completely change the way a mill sources its energy, particularly when coming from wind or solar power. This could mean that a mill could potentially supply its customers with totally CO2-free products.”
One of the big question marks that persists is digitalization being used in the tissue making process. There is now a lot of information about what can be done, but little evidence of digitalization in action.
“It seems that the suppliers have everything in place when it comes to the digitalization of the tissue making process, and the producers are taking it on board,” says Kottwitz, “but where is the evidence of it being used successfully in action? Digitalization has been hyped as the next `big thing’ for too long now; it’s time for the industry to live up to the hype.”