JOHN A. NEUN
In our Jul/Aug 2016 Paper360° article about climate change1, Jim Atkins, Jan Bottiglieri, and I addressed three fundamental resources needed to make paper: fiber, energy, and water. A follow-up article in the Jul/Aug 2018 issue addressed energy use reduction2, and another article in the Nov/Dec 2019 issue tackled fiber sustainability. This article discusses water use on paper machines, why it is important to optimize water use and, finally, some strategies for doing so.
The 2016 article leads to two broad conclusions: the world is changing and thus so is the supply of resources needed to make paper. Water is fundamental to all of those key resources. As the climate becomes more unsettled, unprecedented drought and flooding occur, upsetting normal supply. As the world changes, water will become scarce… or not. Change is inevitable, but direction is difficult to predict. Prudence demands that, in times of uncertainty, prepare for the worst; undoubtedly, “the worst” requires efficient and minimal use of water. Smart use of water inevitably results in improved energy efficiency, too. Using less water is a good way to prepare for the future and save money in the present.
HOW DO PAPER MACHINES USE WATER?
TAPPI TIP 0404-63 indicates3 top performing machines should consume about 1,000—2,000 gallons/ton. About a dozen mills in North America actually have zero water discharge. While not typical, these mills represent the possibility of using much less water and overcoming the challenges in doing so.
A mantra of conservation for a generation has been “reduce, reuse, and recycle.” That’s a good place to start for a paper machine, too.
• Reduce: tune applications to operate with lower volumes of water; and
• Reuse: process water mechanically or chemically to reuse it, replacing fresh water.
Water is the lifeblood of paper machines. A typical headbox can easily flow 30,000 gallons of water per minute (gpm). Most of that water stays on the machine and flows in loops. How much doesn’t—that is, how much is lost—is a fundamental source of inefficiency.
“Typical” is a dangerous word to use to describe paper machines, but consider a broad, “typical” system. Water moves in three large loops (Figure 1). The first is water that leaves the headbox, is drained in the former, and goes back to the headbox as white water. Most of the water that comes to the headbox is white water. Most of the rest (about 20 percent) comes from the high-density stock chests that supply fiber to the machine. Water can escape from the machine loops in a number of ways, both deliberate and inadvertent. The water in the paper sheet lost to evaporation in the dryers by design represents only about 1 percent of the headbox flow.
The second and third white water loops serve two purposes. First, fiber otherwise lost in excess white water is rescued; second, water is captured for reuse. White water is usually processed through some type of barrier filter system (a save-all), which separates fiber from white water and creates filtered water. The second loop uses clear white water for showers and other applications in the wet end of the paper machine, mostly ending up back in the white water chest. The third loop pushes water upstream to pulpers, washers, and cleaners, and downstream to pulpers, especially during sheet breaks. In a perfect system, most of that water theoretically ends up back in the white water system, too.
Water usually overflows from a white water storage chest. Ideally, there would be no overflow, which would require a perfect balance between water entering and exiting the machine. Given the very large volumes and inherent perturbations of the process, such precision is not even remotely feasible. Since the steady-state process is not sustainable with too little water entering, there must be at least some excess/overflow.
Most machines are designed to overflow the lowest value water, which is the water with the least amount of fiber. In Figure 1, that would be from the clear leg of the save-all. In practice, water often overflows from other, richer white water chests. Reasons include inadequate save-all performance (very common for machines that are running beyond their design capacities with aging save-alls), low white water demand, or insufficient pumping capacity, to name a few.
Figure 1 also shows where water and steam can be added to the machine. Ideally, cold water is added only during start-ups. If cold water is added during operation, steam must be added too, to maintain process temperature. Water is added for a number of reasons, such as insufficient white water volume or especially inadequate white water quality.
For example, if machine showers supplied by filtered white water chronically plug and are switched to clean water, less white water is used (making overflow volumes higher) and fresh water is added to the system. As machines age and production increases beyond designed capacity, such anomalies become more common.
HOW MUCH IS WATER WORTH?
The value of lost water has three components:
1. The value of the water itself. Water cost is usually the least important factor for reported effluent value. I have examined many water systems, and the value of water ranges from US$0 per million gallons to about US$3,000 per million gallons. The idea of “free water” is archaic and not realistic; just the cost of power for pumping water to a reasonable storage head is at least US$20/million gallons. If municipal water is used, then cost can be thousands of dollars per million gallons. Typically, mills assess water cost at something like US$200/million gallons. (One million gallons/day corresponds to about 700 gpm.)
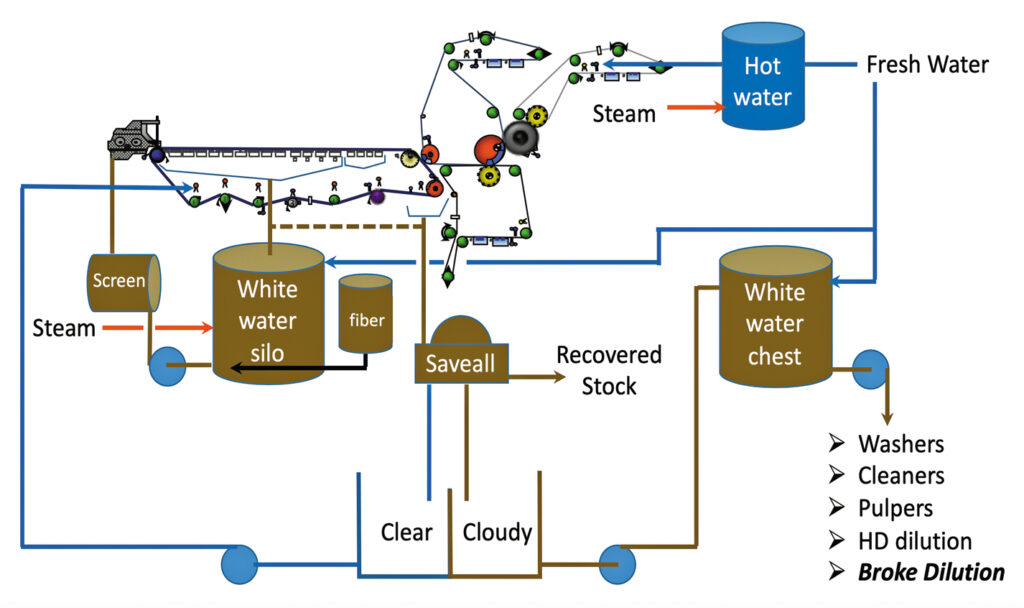
2. The value of the fiber in the water. This number, too, can vary widely depending on the quality of the wasted fiber, fiber retention on the machine, whether production is fiber limited, and how expensive it is to get fiber to the process. If machine fiber retention is poor and overflowed white water is rich, the value of fiber in water can top US$600/million gallons. (This assumes 1,000 parts/million useable fiber at US$150/ton cost.)
3. The heat in the water. If process temperature is important to efficiency—and it always is—then every gallon of cold water added to replace a gallon of warm water lost must be heated. If the process temperature is 130°F and entering cold water is 70°F, it would take about 500 million BTUs to heat the replacement water for every million gallons. Heating is usually accomplished with steam injection in a white water silo. If steam costs US$5/1,000 pounds, the heat is worth about US$2,500/million gallons.
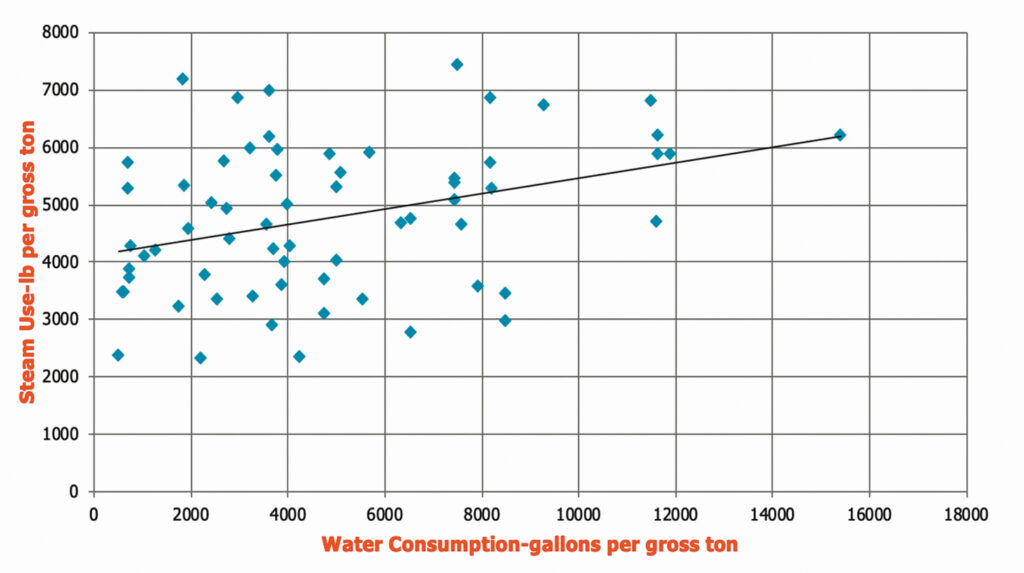
Stated another way, it costs more than US$1,000/year per gpm to heat water by 60°F. Figure 2 shows steam use vs. fresh water use for a large population of paper machines. Despite a lot of variation, there is a definite proportional relationship. Even when the leanest water is overflowed, that water still has heat that must be replaced. This is usually the key to the value of reducing overflow.
In an integrated paper mill, the value of water and effluent may not be so straightforward. Kraft pulp mills generate a lot of excess heat. Some mills have systems to use this heat on paper machines, usually as hot water, eliminating or greatly reducing the need for steam heating. If this energy is not used, it ends up in the atmosphere through a cooling tower or like system at the pulp mill. In this case, from the paper machine perspective, the heat comes at no cost and replacing hot water with recycled white water brings no real energy benefit.
EXAMPLES: WASTING AND SAVING WATER
We’ve discussed in a general way how water is wasted and that some water overflow is inevitable. Here are a few more specific examples.
One baffling indication of paper machine fresh water use is flow while the machine is not operating. Paper machines are large, complicated, and evolved systems with thousands of valves. It is not realistic to expect them all to operate perfectly. Still, the volume of downtime water use, if it is measured, is usually surprising, observed as high as 1,000 gpm. Some of the most common culprits for non-productive water use are: agitator and pump seal lubrication; oil and hydraulic cooling water; hoses; and vacuum pump seal water.
Shaft packing water is easy to overlook because each shaft requires small volumes of water, typically 3 -10 gpm. PMs have a lot of shafts, though, and total volume is hundreds of gpm. This water is almost always left on during shutdowns. To minimize wasted water, packings should be kept in good condition to avoid high clearances. Volumes to each packing should be limited and pressure should be regulated to eliminate excessive flow. Mills can use mechanical, dry seals—they are more expensive, but pay for themselves in the long run. Finally, recirculating systems are available. Usually these systems are justifiable only in applications where water is very expensive.
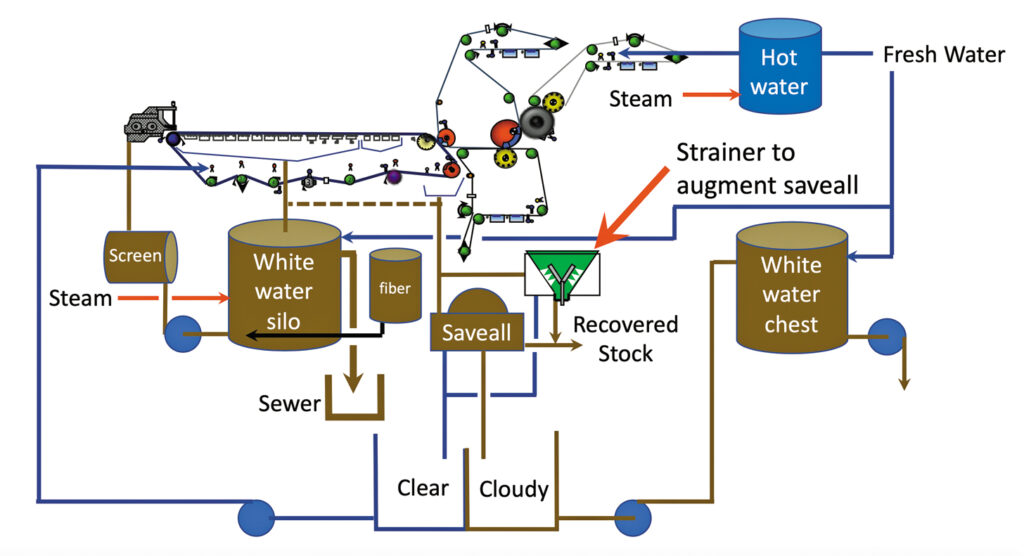
The coldest water available is always used for oil and especially hydraulic system cooling. This is logical because the price of failure of these systems is very high. The water is heated between 100°F and 300°F, which makes it warm but not hot enough to be very useful. Cooling water usually gets added to the hot water system of the paper machine, which makes sense because it is very clean water; but again, there is a thermal penalty to pay. Cooling water typically represents hundreds of gpm. It, too, is often left on during shutdowns.
Wash-up hoses are always located all over a paper machine. Even the best-run machines usually have at least one hose that is left on to flush a stray fiber stream or cool something. These hoses should only be used for wash-up.
Liquid ring vacuum pumps are perfectly suited to papermaking and can be found on almost all US paper machines. They require a lot of water to maintain the liquid ring used to generate vacuum. On a typical 1,000 ton/day machine, demand would probably be about 1,000 gpm. The vacuum pump seal water is inexplicably often not turned off during shutdowns. During operation, it can be circulated through cooling towers and saved, or cascaded from critical to less important pumps to reduce volume.
SOME APPROACHES TO EFFICIENCY
Most US paper machines are not new. Most have run for decades, and most are run at high production rates undreamed of when they were built. If the “free and limitless” paradigm for water is no longer valid, how can we change our approaches to water use? “Reduce and reuse” provides a new, timely approach.
Reduce: Most of the water in the second white water loop we’ve discussed goes to showers. Our example, a 1,000 tpd PM, would probably use about 1,000 gpm or more of shower water. It could get by with about half of that amount. TAPPI TIP 0404-61 provides some reference standards for paper machine showers4.
The highest volume shower on most machines is the flooded nip knockoff shower. It can easily consume half of the shower water on the machine. Modern forming fabrics make flooded nip showers very attractive for reliable sheet knock-off during sheet breaks. Here are two proven schemes to reduce flooded nip shower volume:
1. Reduce shower pressure during operation. High volumes are needed only to knock off the sheet. The flooded nip is a superb fabric cleaning device, but knock-off volumes are not needed for good cleaning.
2. Wash rolls, if properly lubricated and doctored, are proven knock-off devices that work at much lower water, usually less than 20 percent. If the couch pit is configured to accept the sheet after the wash roll, a flooded nip shower can be eliminated.
The next-highest shower water users are lubrication showers, mostly on wire return rolls in the former. The shower standard (see reference 4) defines their required volume as .15 gpm/inch-width. Because they are usually located in the wettest section of the PM, it is rare that they cannot run successfully at half of that volume.
The most critical cleaning showers on the machine are the high-pressure needle showers. These typically use about half as much water as the lubrication showers. There are two effective ways to reduce their required water volume:
1. Use smaller nozzles at higher pressure to save about 40 percent of the water used by the shower with no sacrifice in cleaning efficacy5,6; or
2. Single-jet scanning showers can apply equivalent cleaning power to full-width showers and reduce required shower flow by more than 90 percent.
Sometimes reducing flow is just a matter of finding open valves that should be closed. In a paper mill in Wisconsin we discovered a condenser cooling valve stuck fully open. The subsequent “over cooling” of the condensate cost the equivalent of 2,200 lb/hr of steam to make up for the lost heat.
Reuse: Two critical factors often block the use of white water and consequently cause its waste. These are:
1. Insufficient capacity for filtration of white water to save fiber and create cleaner white water for paper machine use; and
2. Insufficient quality of processed white water for paper machine use, causing substitution of fresh water.
Both of these factors are often immediately attributable to a poorly functioning or overloaded save-all. Often, inadequate save-all operation can be alleviated by adding simpler mechanical filtration devices to both save fiber and create better water for machine use. These strainers can be used in parallel with save-alls, as shown in Figure 3, or downstream of clear or cloudy save-all legs to make better water for use in machine showers. Such approaches have been successful in enough mills to make them state-of-the-art. They can economically help papermaking systems with overloaded or poorly running save-alls.
We found a great example of potential for reuse in a Wisconsin mill. White water was passed over a gravity strainer, where recovered fiber was dropped into the broke chest, and recovered water was used for showers. Unfortunately, the strainer was dysfunctional, so very little water was recovered and white water flowed straight to the broke chest, over-diluting it and causing fresh, cold water to be used for machine showers. In this case, the annual cost to heat the 450 gpm of cold water used for showering was about
US$450,000/year. Replacing the obsolete screen would save this steam cost and reduce excess white water overflow.
It makes sense to save water. Water is a critical and diminishing resource and saving water saves money. There are several extreme examples of very low water volume users in the US, and these mills provide a standard toward which every paper machine can work.
Just wanting to save water can yield results—for example, by turning off water when the paper machine is shut down. Mills can use other techniques to reduce a typical paper machine’s water consumption considerably. These techniques range from simple to expensive, and will be increasingly important to many mills that face shortages of water in the foreseeable future.
References:
1. Climate Change and Its Possible Effects on the US Paper Industry, Atkins, Bottiglieri, Neun, Paper360°, July/August 2016.
2. Reducing Energy Use, Reese, Paper360°, July/August 2016.
3. TAPPI TIP 0404-63, “Paper Machine Energy Conservation”.
4. TAPPI TIP 0404-61, “Paper Machine Shower Recommendations”.
5. “Dynamics of Energy Transfer from a Shower Jet,” Baldauf, Harper, 1994 TAPPI Engineering Conference, San Francisco.
6. “On-line Cleaning of Dryer Fabrics,” Neun, 1996 TAPPI Engineering Conference, Chicago.
John A. Neun, P.E. is subject matter expert (mill water systems) for Clean Tech Partners. Since beginning his paper industry career in 1979, Neun has been a frequent presenter at industry conferences and has published many technical papers in his areas of expertise. He is a TAPPI Fellow and received the Engineering Division’s 2018 Technical Award & Beloit Prize recognizing his paper and tissue work and contributions globally. Reach him at [email protected].