TOR IDHAMMAR, IDCON
Did you know that the US contains 5 percent of the world’s population and 75 percent of all the lawyers in the world? I’m not sure why this is, but I’ve noticed that companies and people sue each other more often in the US than in many other countries. There may be some positives as well as negatives of having all these lawyers around; perhaps it is just hard to see the benefit sometimes. I do think the risk of getting sued has made companies overly cautious in their collaboration and information sharing efforts. I also think the lack of information sharing hurts our industry because we don’t use the benefit of collaboration much at all.
An example of a missed opportunity in cooperation is what we call “Preventive Maintenance Cards” or “PM Cards” for short. The PM Card is a summary and standard for all preventive maintenance actions that need to be done for a component. We call a “component” something that is highly repetitive on the plant floor. For example, an AC motor is a very common component, as well as a centrifugal pump or gear coupling.
My thinking is that Domtar, International Paper, Kimberly-Clark, and other paper companies have the same couplings, the same AC motors, etc., but they don’t have the same PM cards. Why not? Granted, the application could be slightly different—a motor could run 24/7, or only one hour a day, for example—but in general, the applications are very similar. Perhaps an even more interesting question is why we don’t have the same PM cards or even PM standards within a single company with several similar mills?
IDCON has worked on PM cards and standards for more than 45 years. We coach, write, and recycle our knowledge going from mill to mill using different formats and approaches depending on our clients’ perceived needs and wishes. This is great business for us, but it’s pretty wasteful. It is not uncommon that we set up PMs for the same mill several times due to changes in management and systems.
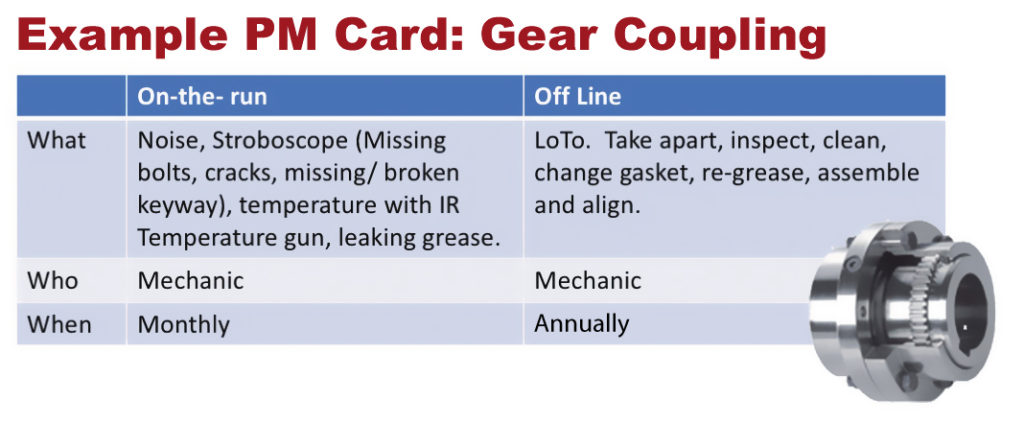
So, if a company would adopt a PM standard format and then communicate it within the company—perhaps even within the industry—there is a lot of money to be saved. There would be even more money to be saved if paper mills actually executed their PMs and repaired the problems found during PM routines, but that is a subject for another article!
A great PM program will increase product output, improve product delivery reliability, lower manufacturing cost over time, extend the life of the equipment, and create a well-maintained mill that is safer to work in.