Forming of the paper sheet is the most critical phase in the paper production process. Cleanliness throughout the operating life of the forming fabrics is critical to maintain high paper quality. A clean forming fabric, with consistently high permeability and dewatering capabilities, delivers important productivity and performance advantages. Better dewatering in the forming section leads to substantial improvement in dryness level when the sheet leaves the wire section and moves into the press section.
Forming fabrics lose dewatering ability when contamination builds up over time. More and more contamination can be found on forming fabrics caused by an increasing use of secondary fibers, recycling of coated broke, increasing use of sheet fillers, an increased use of recycled mill water supplies, and the increased use of process chemicals. Typical contaminants are wet strength resins, retention aids, stickies, scale, de-foamers, calcium carbonate, clay, starch, and alkaline size.
Typical “stickies” on a forming fabric.
CONTROLLING MACHINE CLOTHING CONTAMINATION ON TISSUE MACHINES
Controlling contamination on a tissue machine is critically important. A customized cleaning program for paper machine clothing (PMC) will keep the tissue machine running efficiently and producing high quality tissue.
A tissue crescent former forming fabric and press felt are relatively short and run at high speed, making effective cleaning more challenging. In combination with the industry trend to use more recycled fiber, this results in unique cleaning requirements for tissue machines.
Typical contaminants found in tissue clothing are similar to those previously mentioned for paper machines. Additional contaminants for tissue include paper fines, Yankee coatings, and rust.
The biggest cleaning challenge for forming fabrics are stickies and other contaminants that are not water-soluble. These contaminants start to collect in the machine clothing’s yarn crossover points. Once small particles (stickies) attach, they attract other stickies and they start to conglomerate. While these conglomerates are growing, they will increasingly affect the drainage path of the fabric, eventually leading to holes in the sheet.
Most high-speed tissue machines use triple layer forming fabrics that provide the best sheet formation on the sheet side and longer life for the inner layer of the fabric. Sheet dewatering occurs when the press felt transfers water from the sheet to the press through microscopic voids in the felt. Water transfer can no longer occur properly when the channels are blocked with contaminants or gels. Properly cleaned press fabrics maintain their voids and provide consistent dewatering performance throughout the fabric’s life. This has a positive effect on dewatering efficiency, energy use, sheet profile, sheet bulkiness, and press felt life.
CONVENTIONAL CLEANING METHODS
Cleaning methods can be classified as chemical or mechanical; while chemical cleaning is becoming less common, it is still required for certain conditions. Mechanical cleaning (with high pressure—HP) is the most widely used method. The conventional cleaning method comprises an oscillating HP shower on the sheet side and a flooded nip shower on the inside.
Typical pressure varies between 15-40 bar (230-600 psi) and typical nozzle size is 0.8-1.0mm (.032″-.040″). Depending on number of nozzles and sheet width, this leads to water consumption between 100.0-250.0 ltr/min (25.0-100.0 GPM). Typical power consumption of the HP pump for these showers is 40.0-80.0kW (50.0-100.0hp).
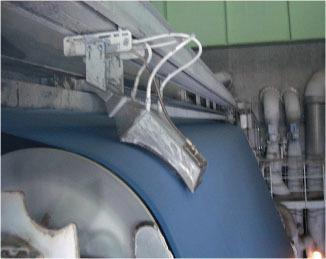
THE TRAVERSING HEAD SHOWER
ProJet, a company from the Netherlands, has developed a new cleaning technology called ProCleaner™. Using a multi nozzle traversing head, this new method has some unique advantages over traditional HP showers. The ProCleaner is located on the sheet side at an inside return roll.
Applying a ProJet ProCleaner guarantees consistently clean forming fabrics and press felts from beginning to end of the usable life. This delivers the following significant advantages over conventional showers:
- In most cases, conventional HP showers can be switched off, leading to water consumption savings of up to 90 percent.
- Up to 80 percent lower power consumption by the HP pump.
- PMC life will be substantially improved.
- Fewer shutdowns will be required for manual and chemical cleaning, as well as for PMC changes. This will provide increased manufacturing productivity and profitability.
- Maintaining consistently high forming fabric and press felt permeability and dewatering capabilities increases dryness of the sheet when leaving the wet section and entering the dryer section.
- Capability for programing “zone cleaning”: targeted cleaning of contaminated zones in the cross-machine direction.
- Reduced number of sheet breaks caused by contaminated PMC.
- Water mist elimination, achieved by the application of air knives that restricts water mist and contamination, which is then discharged through Venturi tubes and finally into a save-all pan.
- The system has a Park Position outside the machine, which enables maintenance such as nozzle and filter changes during production.
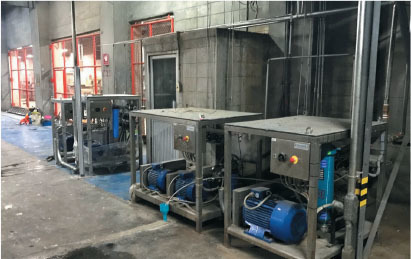
FLEXIBLE PARAMETERS
The ProJet ProCleaner is designed with maximum flexibility to adapt to every machine situation, paper grade, furnish, and required cleaning conditions. ProJet has designed the pump station and control system to let operators choose the optimum set of parameters:
- Traversing speed: This can be synchronized with the machine speed so maximum coverage is achieved and overlapping of nozzles is minimized.
- Cleaning width: The cleaning head is equipped with an encoder so the head can be sent to certain areas of the felt that can then be cleaned more intensively for a certain period of time before returning to full width cleaning. Customers have identified this as a problem-solving tool when other disturbances in the production process create dirty streaks on the felt.
- Pressure: The pump is designed to have a maximum pressure of 240 bar (3,500psi). This allows the system to run with higher pressure and smaller nozzles.
- Nozzle size: The nozzle size is typically between 0.2-0.3mm, but can be varied to optimize cleaning efficiency.
Of course, each client application is unique. For that reason, ProJet developed an automated ROI calculator that will be applied to each application and produced paper grade. ProJet will perform a complimentary ROI calculation of any forming fabric, press felt, or dryer fabric application. After inputting the process parameters provided by customers, they will be provided with an ROI analysis of each specific application and investment justification.