GEORGE BOWER
Developing a strong safety culture requires a commitment to safety excellence at all levels of an organization. However, many organizations (or even facilities/departments within an organization) find it quite difficult to optimize their safety identity.
THE STRUGGLE IS REAL
Why do so many struggle with this? It’s certainly not because there is an easy answer, as those of us within safety and/or management can attest to. However, let me offer a few potential drivers:
• Lack of leadership
• Lack of accountability
• Lack of competence
• Lack of buy-in (possibly due to one of the above)
Of the four listed above, leadership is most often identified as having the strongest affect on an organization’s safety culture. Without effective leadership and supervisor involvement, it is virtually impossible to develop a strong safety culture.
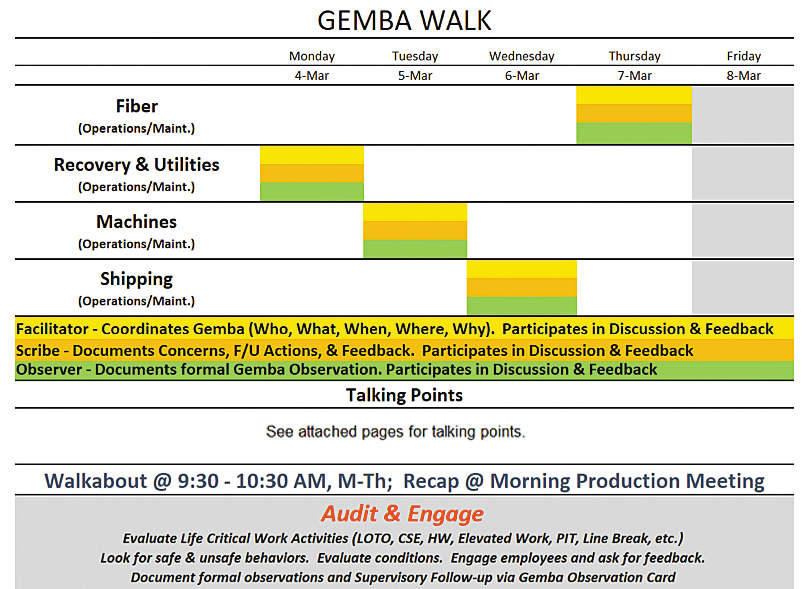
Effective leadership, throughout all levels of an organization, increases worker engagement and reemphasizes a commitment to safety, which leads to a reduction in incidents and subsequent injuries. Without a commitment to effective leadership, no matter how strong your safety culture seems to be, the message will not trickle down to the line employees. While there are a multitude of references and plenty of research on being an effective leader, one of the most effective methodologies is the “gemba walk.”
‘GO TO THE GEMBA’
Gemba, a Japanese word meaning “the actual place,” refers to the place where value is created. In the case of pulp and paper (as with other manufacturing operations), this is the floor. Toyota, known for its manufacturing excellence, developed the gemba concept as a way to identify wasteful activities. Within safety, we can certainly translate “waste” as unsafe conditions or activities that lead to inefficiencies (slow or stop work, injury, illness, etc.)
Gemba centers around getting out there, seeing and being seen, interacting, communicating, and identifying safety issues and concerns. It provides an opportunity to be involved and develop relationships between leaders and employees. A gemba walk creates a real opportunity to solicit buy-in, exhibit competence, increase accountability, and ultimately demonstrate leadership.
STANDARDIZE THE PROCESS
How can an organization begin to “go to the gemba”? The following provides an overview of the framework needed to develop the process.
1. Commit to the WHAT: Effective leadership equals a safer work environment. One method of increasing effective leadership is the gemba walk.
2. Understand the WHY: The goal is to develop or increase the safety culture within your organization by having management and leaders “on the floor” to determine where the inefficiencies (i.e., hazards and risk) lie.
3. Determine the WHO: Which employees should be involved? Develop small teams of three or four people of various levels within the organization or facility. Include senior management, supervisors, front line leaders, and those persons who routinely interact with line employees.
4. Know the WHERE: Find where the snakes are hidden. Don’t just “go to the gemba” in the high-traffic areas. Ensure that your gemba includes the “roads less travelled.” You would be surprised by the safety value and input (i.e., buy-in) your organization can receive by performing gemba walks at near 100 percent coverage.
5. Develop the WHEN: Set a schedule to include who will be involved, when the gemba walks will occur, what areas will be included, and the typical time allotted to complete the walk (typically 30 minutes to an hour).
6. Establish the HOW: Performing the gemba walk is the first step; defining HOW you’ll get value out of it is based on your reporting mechanism. Set expectations on when and how you’ll report out and what you will do with the findings or issues requiring follow-up. Additionally, this reporting mechanism provides a measure of accountability for the expectations set forth for the members of the gemba walk.
EFFECTIVE LEADERSHIP IS HABITUAL
Over time, the standardized process can and should evolve. Standardizing should only serve as a guide to get leaders started, until “going to the gemba” becomes habit and competence increases. Habitual, effective safety leadership translates into an improvement in safety culture and, most importantly, keeping our employees safe.
George Bower, CSP, CIH, is a senior safety and industrial hygiene consultant with S&ME, and former safety director for a large Southeastern paper mill. If you are interested in learning more about making your safety leadership more effective through the gemba process, contact him at [email protected]. This article is provided with the support of TAPPISAFE. Visit tappisafe.org to learn more.