Sappi Europe’s Largest Mill Accelerates Decarbonization Efforts
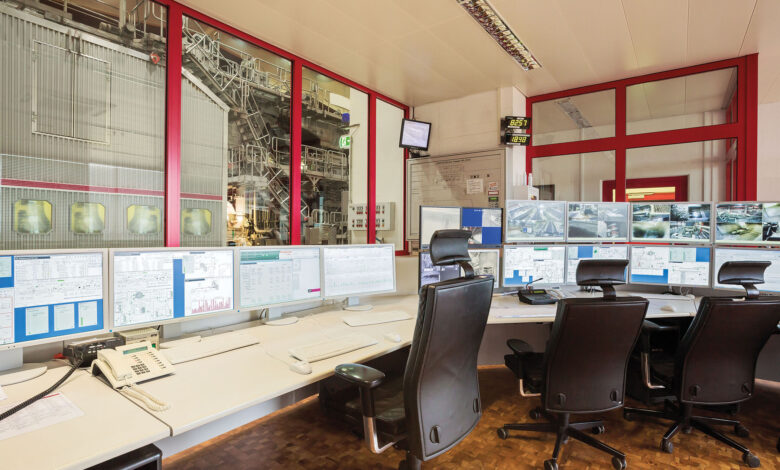
GEORG NIEDERHAUSER
Despite the relentless digitalization of the world’s economy and the pandemic’s continuing adverse market impacts on the pulp and paper industry, renewed demand is expected to restore growth in the most affected segments as schools, offices, restaurants, and other public venues reopen to the so-called “new normal.” During the past year-and-a-half’s unprecedented times, one industry imperative remained: the need to decarbonize production.

Of course, the reason is emissions-driven climate change. According to the US National Oceanic and Atmospheric Administration (NOAA), the seven warmest years in the 1880-2020 record have occurred since 2014. In fact, 2020 was Earth’s second warmest year ever, behind 2016.1 And that’s notwithstanding the substantial cooling effects of last year’s vast La Niña phenomenon over the Pacific Ocean’s tropics. Its cooler temperatures were more than 2.5 times the 70-year average.2

As a whole, the world’s pulp and paper industry ranks fifth in its greenhouse gas emissions, primarily due to the substantial energy used in production.3 The good news is how much progress the industry has made in decoupling rising energy use from production growth. From 2000 to 2018, global paper and paperboard output rose more than 25 percent while energy use increased by only 6 percent. Part of that decoupling was due to greater energy efficiencies in mills and plants, while the rest was due to the use of recycled fiber, which cuts the industry’s energy intensity.4
MORE INDUSTRY EFFORT NEEDED
Yet for all this progress, tracked by the International Energy Agency (IEA), the industry is urged to increase its recycling and expand the use of bioenergy and waste heat recovery to use even less energy. To that end, in 2020, Sappi announced that it would make the United Nations Sustainable Development Goals (UN SDGs) an integral part of how it does business—to unlock the power of trees to make every day more sustainable for the customers Sappi serves, the communities where it operates, and the planet we all call home.
As part of Sappi’s commitment to helping the pulp and paper industry do its part to reduce global emissions, Sappi’s specific 2025 targets include the following:5
• Boost the amount of renewable energy used in operations worldwide by 9 percent;
• Reduce total energy use by 5 percent;
• Decrease specific greenhouse gas (GHG) emissions by 17 percent;
• Increase share of certified fiber in products to more than 75 percent.
To accelerate Sappi’s pace to achieve these and other UN SDGs, Sappi Europe has partnered with Siemens Energy to implement the latter’s SIPAPER process control technology as part of an extensive modernization project at its paper mill in Gratkorn, Austria. This plant is Sappi Europe’s largest and produces about 990,000 tpy of high-quality, wood-free paper for the global printing and stationery market.
In recent years, Sappi has made several investments at the Gratkorn mill to ensure its technology stays up-to-date. For example, the mill’s coated fine paper production line is one of the largest and most modern worldwide. It uses 250,000 tons of totally chlorine-free (TCF) pulp as an intermediate for other products made there.
The mill retrofit is scheduled to be performed in two phases and be completed in the first quarter of 2022. The new process control technology will support the process to make production more environmentally friendly, resource-efficient, and profitable.
TOWARD A LOW-CARBON FUTURE
“The investment is part of a long-term strategy to decarbonize Sappi Europe’s production processes at all its plants in the region. One step in decarbonizing the Gratkorn plant’s operations is converting its 30-year-old steam boiler, which supplies two paper machines with steam and power, from being coal-fired to using multiple fuels,” says Max Oberhumer, Sappi Austria GmbH. “In the first phase, the boiler will be converted to natural gas, then in a second phase, to biomass. This will enable the plant to reduce the boiler’s CO2 emissions by 30 percent initially, with the ultimate goal to produce steam and power that is primarily CO2-neutral.”
The next step in the Gratkorn plant’s modernization and decarbonization is to increase the end-to-end digitalization of production to make it more eco-friendly and efficient using intelligent process control systems and energy-efficient drive systems, integrated engineering, and optimized plant design. This will provide greater operational visibility and better automate the many and myriad interlocking systems and their processes.
In planning the Gratkorn plant’s modernization, the respective Siemens Energy and Sappi engineering teams worked in close collaboration, considering the plant as an integrated whole—a critical step toward plant optimization. The failure or underperformance of one asset can affect another or many others. While many pulp and paper plant engineers may recognize this dynamic in theory, it often can be difficult to recognize in practice, with the downstream effects of one asset’s sub-optimal operation creating hidden costs.
For example, when particles fly up from a recovery boiler into superheated sections due to poor combustion, steam can be wasted to blow out the soot instead of pushing it into the turbine. Or, superheated steam can damage the evaporator, emit condensate, and build up deposits in the boiler tubes and steam turbine. This can cause a loss of heat transfer and power generating efficiency.
HIDDEN INEFFICIENCIES DRIVE
COSTS AND EMISSIONS
These losses can quickly accumulate and result in hidden costs—and unnecessary emissions. Consider this: For every micrometer of buildup, some 250 kilowatts of energy are lost. Similar inefficiencies and costs occur when assets are poorly integrated, or not integrated at all. In some pulp and paper mills, roughly EUR2 million per year (about US$2.44 million) is lost because the turbine and the black liquor boiler are not being operated and synchronized by the same process controls.
Another opportunity to reduce energy use has been to add, upgrade, and automate the use of variable frequency drives (VFDs). These operate the many hundreds of electric motors operating pumps, blowers, fans, and other rotating equipment throughout production.
In Siemens Energy’s experience, fuel and electricity account for about 20 percent of pulp and paper production costs. Of that, on average, pumps consume around 25 percent of power, compressed air around 16 percent, and fans around 13 percent. Ultimately, over a motor’s service life, 95 percent of the total cost of ownership is energy costs, with acquisition and installation capital costs only 5 percent.
By precisely tuning motor speeds to real-time process requirements and ambient plant conditions via motor sensors and intelligent automation, wasted energy can be reduced, if not eliminated. Motor life can be extended, while maintenance can be shifted from a disciplined, scheduled model to a more fluid, predictive, and proactive model. The latter saves shop-floor labor and expertise for more value-adding tasks.
In parallel with maximizing all possible energy efficiencies—and as part of the modernization of the Gratkorn plant’s boiler—the modernization team deployed a new process control system based on the SIMATIC PCS7 controller with ET200SP HA I/O peripherals as well as the SIPAPER DCS APL library of proven code. This decentralized, distributed control system (DCS) provides a scalable, uniform, and fully integrated automation model, from the production floor’s field level up to its ERP level. With it, the plant operations staff has full data transparency and diagnostics to optimize processes and minimize downtime continually.
As mentioned, the Gratkorn plant modernization is on track for completion early next year. Sappi and Siemens look forward to accelerating progress toward a low-carbon future that can serve as a model to the entire pulp and paper industry.
References:
1 Global Climate Report—Annual 2020. U.S. National Oceanic and Atmospheric Administration.
2 Emily Becker. “November 2020 La Niña Update: Just Us Chickens.” U.S. National Oceanic and Atmospheric Administration. November 12, 2020.
3 Hannah Ritchie and Max Roser. Our World in Data: Emissions by Sector. 2016.
4 Peter Levi et al. “Pulp and Paper: Tracking Progress 2020.” June 2020.
5 “New sustainability targets for a thriving world.” Sappi Group. 2020.
Georg Niederhauser, Siemens Energy Austria GmbH, was born in Tyrol, Austria. He has worked at Siemens (now Siemens Energy) since 1989 and is currently the head of vertical fiber industry, CEE for Siemens Energy Austria GmbH.