PM Upgrade Requires a Comprehensive Condition Monitoring Solution
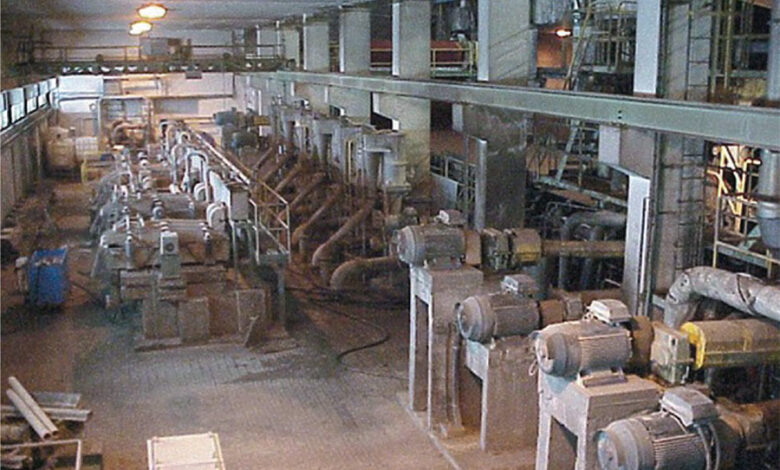

In the pulp and paper industry, production is directly related to the paper machine speed. For older paper machines originally designed to operate at slower speeds, attention is being given in the mills to increase the rate of production. In the following case study, mill leadership decided to nearly double the production speed—but this required modifications to the paper machine. To ensure machine reliability, the mill installed a condition monitoring system to monitor the rollers to ensure that the bearings were not overstressed.
THE CHALLENGE
An eastern European paper mill decided to upgrade its paper machine to produce more containerboard to fulfill market demand. To achieve this, mill management set an ambitious target: the production speed was to be increased from the original speed of 180 m/min to 300 m/min.
After performing a detailed analysis of the aging machine, the team determined that only the first four dryer sections needed to be modified to accommodate the higher speed. From an operational point of view this was an optimal solution, but the maintenance manager knew there was a risk that the unmodified sections of the paper machine would be stressed at the higher speeds.
The mill team decided to work with Brüel & Kjær Vibro (B&K Vibro) to implement a condition monitoring solution. Consisting of an advanced monitoring system and long-term service, this comprehensive monitoring solution would detect and diagnose a wide range of potential failure modes. It would allow the mill to keep a better eye on the asset—not only after the full speed implementation of the plant machine upgrade, but also including the transitional phase in gradually bringing the machine up to full speed.
Founded in 1942, B&K Vibro supplies advanced technology for monitoring and managing vibration. The company maintains a network of sales and service offices worldwide.
THE SOLUTION
The mill began by identifying the components it considered the most vulnerable with regard to machine stress and gave these components the highest priority for online monitoring. As a first step, the online condition monitoring solution focused on:
- The entire dryer section of the PM, consisting of four individual units; and
- five liquid ring vacuum pumps for extracting water from forming section and the felt Uhle boxes in the press section.

In addition to the online system, the mill used B&K Vibro’s vibration monitoring handheld device for monitoring the auxiliaries. The mill also planned to extend the online monitoring solution to the forming, press, and calendar sections at some point in the future.
One important requirement of the monitoring strategy was to automatically monitor the paper machine under all operating conditions as the speed was gradually increased over time, without needing to reconfigure the system. This is because the vibration signature of a component changes with speed, and therefore static alarm limits could result in false alarms or unseen alarms as the speed changes. The monitoring system successfully fulfilled this requirement because individual alarm limits could be set up for different speed ranges that automatically change as the speed changes.
The monitoring strategy also needed to consider a number of potential failure modes that can occur in the machine components, as well as a range of vibration related runnability issues such as barring and resonances. To meet these requirements, the B&K Vibro system offered application-specific broad band and narrow-band monitoring techniques that could easily be configured for the specific components and operating conditions; and reliably and quickly fine-tuned over time as mill crews gain experience. A B&K Vibro service was also included to facilitate the transition period of running the paper machine up to speed by providing diagnostic support and measurement technique refinement.
FAULTS DETECTED
The paper machine had passed its transitional phase and had been successfully operating at the maximum speed of 300 m/min. Production of paper and corrugated containerboard had increased from 65,000 tpy to 105,000 tpy. However—just as the maintenance manager feared—the older, unmodified parts of the machine were indeed stressed and a number of faults were detected during this period. After a little more than a year, the system detected the following faults:
- Damaged impeller of the liquid ring vacuum pump
- Gearbox pinion bearing fault
- Roll bearing fault (on four different rolls)
- Excessive clearance in liquid ring vacuum pump bearing
- Cracked piping of the liquid ring vacuum pump
All damaged components were detected early enough to schedule maintenance for the planned shutdown. Assuming six hours of downtime required for each roll bearing that fails outside the planned shutdown periods, that means there is a total of 24 hours in lost production saved by just detecting the four rolls with bearing faults within the first year. This does not include the downtime savings for the pumps. Immediately after the transition period, plans were already underway on extending both the online and handheld monitoring systems to other paper machine sections.

TEACHING AN OLD PM NEW TRICKS
Some mill operators may insist that, because their older machines were over-designed and operate at constant load and speed, they have no need for a predictive maintenance strategy. However, this case study demonstrates that an upgrade on an older machine can completely change that picture. In fact, an upgrade often pushes the operational limits envelope of the machine further out from the previous normal operation. This can therefore result in some components being overstressed and carry with it a greater risk of premature failure. The five component faults detected by the monitoring system after the upgrade proves this.
An effective machine condition monitoring system is not only used for detecting normal wear and tear of machine component faults so maintenance can be planned accordingly, but also for detecting prematurely failing components that are stressed more than normal due to operational conditions. The same monitoring system can also detect unexpected faults, such as incorrect component type replacements, incorrect assembly or installation of components, or components with hidden defects. An effective machine condition monitoring strategy plays a vital role in all aspects of paper machine health care.